Theory of Bending |
The principle of bending in itself is not very difficult to understand. And yet a lot of know-how and skills are required if the technique is to bring maximum productivity and quality. Ultimately, it is primarily a combination involving the geometry of the top tool (with the punch angle and punch tip radius the most important parameters), the geometry of the bottom tool (the width of the V opening, the V angle and the bending radii of the V opening in particular), and the pressing force and speed of the press brake. Naturally, all of these as related to the nature and thickness of the material and the desired bend angle and bend radius of the product. The choice of tool material is another aspect that must be considered. In order to fully understand all of this, we will briefly dive into the theoretical background of bending.
|
|
Bending By Folding
When bending by means of folding, the longest leg of the sheet is clamped between clamping beams, after which the bend beam rises and folds the extending sheet part around a bend profile. With many of today’s folding machines, the bend beam can bend both upwards and downwards, which is a significant advantage in particular for complex parts with both positive and negative bend angles. The resulting bend angle is determined by the folding angle of the bending beam and by the geometry of the tools and the properties of the material. The advantage of bend by means of folding is that large sheets can be handled more easily, in turn making this technique easier to automate. What is more, the risk of damage to the sheet metal surface is minimal. A limitation, however, is the fact that the movement of the bend beam requires the necessary space and throughput time.
|
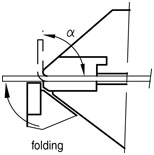
|
Bending By Wiping
With wiping, the sheet is also clamped after which the tool bends the protruding part of the sheet around the bend profile by moving up and down. Wiping is faster than folding, but because the tool moves over the surface of the material, the risk of scratches and other damage is much greater, especially if sharp angles are involved. This technique is particularly popular for making panel-type products with small profiled edges. Using special tools, wiping can also be done on press brakes.
|
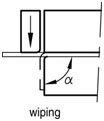
|
Four Variations Of Bending
Bending is the specific topic of this Guide, and this technique will therefore be discussed in more detail. In bending, a distinction can be made between four variations: air bending, bottoming, coining and three-point bending. Characteristic of all of these is the fact that the sheet is pressed by a top tool into the opening of the bottom tool. As a result, both sheet metal parts are lifted, and this can cause problems such as sagging and folding with large sheets. In that case, folding or wiping is preferred, although sheet-follow supports can also be used with the press brake during the bending process. In cases involving both positive and negative angles, bending by means of folding offers more flexibility. The significant advantages offered by press brakes are increased speed and flexibility.
|
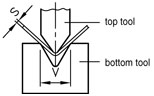 |
Air Bending
With air bending, the top tool presses the sheet into the V opening in the bottom tool to the pre-determined depth, but without touching the bottom of the tool. This is a kind of three-point bending, by which only the bending radii of the top and bottom tools come into contact with the sheet. The punch radius of the top tool and the V angle of the bottom tool need not be the same. In some cases, the V opening in the bottom tool is replaced by a square opening; this is especially the case with today’s adjustable bottom tools. The combination of top and bottom tools can therefore be applied universally, meaning that with a single combination, various products and profile shapes can be produced simply by adjusting the press stroke depth. In other words, with a single combination of tools, multiple materials and thicknesses can be bent in a range of bend angles. This makes air bending a highly-flexible technique. It also means that the number of tool changes can be limited considerably, enhancing productivity. Another advantage is that less bend force is required. As a result, the tools can have a slender shape, offering extra allowance in the design. The machines can also be made lighter and thus less expensive. A limitation presented by air bending is that it is less precise. The stroke depth must have a very high accuracy and variations in sheet thickness as well as local wear on the top and bottom tools can quickly result in unacceptable deviations. Variations in the material properties also affect the resulting bend angle due to the springback that occurs. In order to achieve maximum angle accuracy, a value is applied to the width of the V opening ranging from 6S (6 times material thickness) for sheets up to 3 mm thick to 12S for sheets of more than 10 mm (Rule-of-thumb: V=8S). The angle accuracy possible with air bending is approximately ±30’. Unlike with bottoming and coining, the bend radius is not determined by the shape of the tool, but is dependent on the elasticity of the material. Normally, the bend radius is somewhere between 1S and 2S. Based on it is high flexibility and relatively low tonnage requirements, the market – meaning the sheet metal fabrication industry – is moving more and more towards air bending as the preferred forming technique. The disadvantages involved in this technique in terms of quality are remedied by taking special measures (e.g. angle measuring systems, clamps and crowning systems that are adjustable along both the x and y axis, and wear-resistant tools).
|
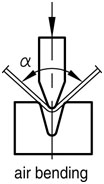
|
Bottoming
Bottoming is a variation of air bending in which the sheet is pressed against the slopes of the V opening in the bottom tool. An air space continues to exist between the sheet and the bottom of the V opening. In this case, the punch radius and the angle of the V opening are directly linked, meaning that bottoming does not offer the same flexibility as air bending. Every bend angle and every sheet thickness requires a separate tool set, and the same often also applies for different materials (due to the springback differences and the compensation required in the tool. The optimum width of the V opening (the U-shaped openings cannot be used in this case) is 6S for sheets up to about 3 mm, increasing to 12S for sheets more than 12 mm thick (Rule-of-thumb: V=8S). The minimum acceptable bending radius for sheet steel runs the range from 0.8S to 2S, although the quality of the material also plays a role. (With a soft material such as copper, the radius of the bend angle may be much smaller: a lower limit of 0.25S is possible.) The required tonnage with bottoming is generally the same as air bending for larger bend radii, but with smaller radii the level of force required may be up to five times higher. However, the advantage is greater accuracy. The resulting bend angle is wholly determined by the tool, with the exception of springback, for which a correction can be made. (The springback is somewhat less in bottoming than in air bending.) Summarizing, angle accuracies of approximately ±15’ are theoretically possible with bottoming. Because the control and adjustment possibilities on press brakes have increased considerably, even on less-expensive machines, bottoming is losing more and more ground to air bending.
|
Coining
With coining, the sheet material is ‘crushed’ by the top tool into the opening of the bottom tool, down to the bottom of the V opening. Coining requires many times the bend force of air bending and bottoming. Normally, five to ten times higher tonnage is required, and in some instances, even 25 to 30 times higher than air or bottoming. The advantage, however, is the high level of precision. Because of the extremely high pressure exerted on the punch tip into the material, permanent deformation occurs throughout the entire cross-section of the sheet, and springback is virtually reduced to zero. As the punch and V-die angle are identical, the desired bend angle can be easily selected. Variations in sheet thickness and the properties of the material have little or no affect on the bending results. Because of the high level of force involved and the permanent deformation that takes place, the minimum inside radius that can be achieved is less (starting from 0.4S) than with air and bottoming. The width of the V opening required is usually about 5S. A wider V opening would mean that its depth must be greater in order to achieve the same bend angle, and this has an unfavorable effect on speed and for this technique are also in a higher price range. Coining is therefore only sporadically applied today, and even then only for thin sheets.
|
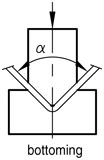 |
Three-Point Bending
A relatively new bending technique is three-point bending, even though some consider it to be a special variation of air bending. This technique, developed by the Swiss company Hämmerle, involves a special die, the bottom of which can be precisely adjusted in height by means of a servomotor. The sheet is bent over the bend radii of the die until it touches the bottom; the bend angle decreases as the depth of the die bottom increases. The bottom level of the die, as already indicated, can be determined very precisely (± 0.01 mm / ± .0004”), and corrections can be made between the ram and the upper tool using a hydraulic ‘cushion’ to compensate for deviations in the sheet thickness. As a result, bend angles with a precision of less than 15’ can be achieved. Advantages of three-point bending are high flexibility combined with high bending precision. Obstacles, however, are the high costs involved with this system and the limited range of available tools. As a result, this technique is limited for the time being to highly-demanding niche markets where the additional costs are outweighed by the advantages.
|
|
|
|